A Warm Shop (Again)
Category: WoodshopDate: 2023-03-11
When we built the shop in 2008, I included radiant floor heat in the design. It's a premium feature and I've never been disappointed in that decision. Not even on February 5, 2023, when the water heater serving that system failed.
Taking care of that failure was a challenging and worthwhile project. Five weeks later the floor is a comfortable 74 degrees, again.
The beginnings
My enthusiasm for radiant floor heating systems comes directly from my experience in the 1980s at Grant County Public Utility District. I initially worked in the Energy Conservation Department with Tom Sinnard who was a huge proponent of radiant floor heating systems. Of course, at the time in Grant County, Washington, radiant floor heating was electric. 30 years later in Utah, my system would be hydronic with a natural gas heat source. After considerable research I settled on a system provided by Radiantec of Vermont. They worked with me to design a system specific for the shop. It was delivered to me as a kit, and I put it together with a large water heater obtained locally. Prior to pouring the slab for the shop, five circuits of PEX tubing (about a half mile in all) were laid out to be imbedded in the concrete floor.
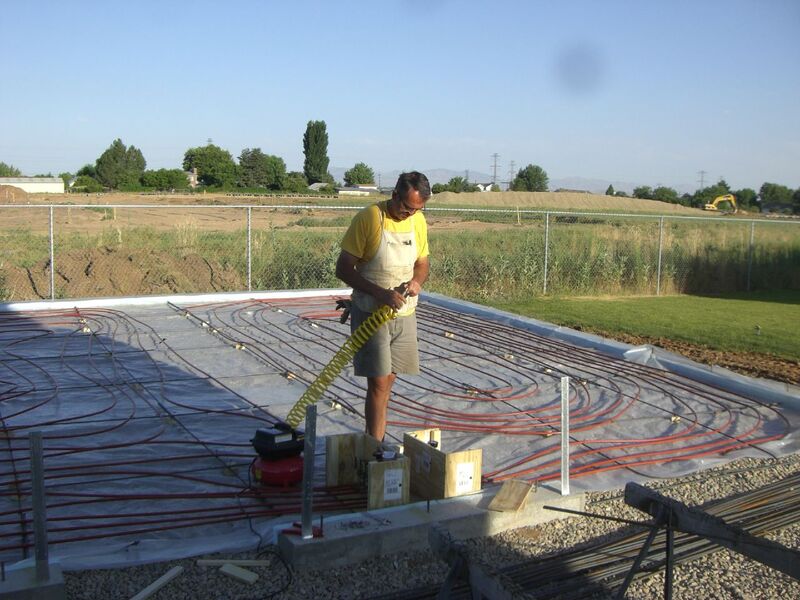
At the time, I wanted to maximize floor space on the main floor. I also wanted to isolate the flame source of the natural gas burner from the dusty shop. So I chose to place the water heater for the system in the upstairs space. I was younger then and placing a 300 pound water heater on the second floor seemed entirely reasonable.
A fateful conversation
In the intervening fourteen years, Terri has claimed all of the upstairs as her lovely craft room. Sometime in January while visting with her up there I said that I thought it would be a good idea to install the water heater downstairs when it failed. Then on the night of Sunday February 5, it failed and gave me the opportunity! Never assume that mechanical systems are not listening.
Repair adventures
The good news is that the woodstove I installed in 2008 can easily heat the well-insulated shop. That Monday morning I placed a priority on finding a supply of firewood, and by the afternoon, I had a pickup load of nice, dry 2x4 cutoffs from a truss plant.
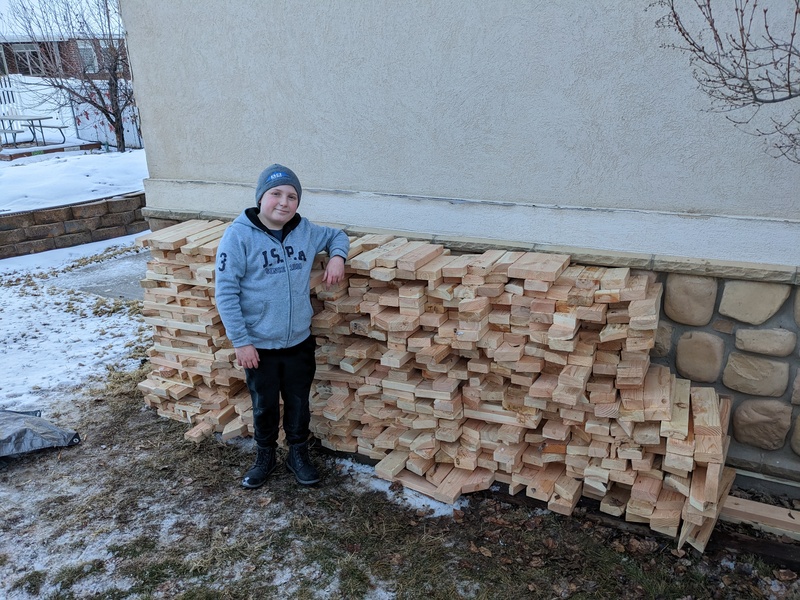
After securing the alternate fuel, I made an appointment with a plumber for the repair of the water heater. As it turns out, that was an expensive mistake. After the repair, I determined that the water heater was done. Finding a replacement 75,000 BTU water heater was an unexpected challenge. I learned that Utah has the nation's most stringent requirements for Nitrous Oxide emissions from water heaters. The plumbing company that I might have hired to replace the unit reported that they could not find a source of a suitable water heater that they could install for less than $6000. That was a non-starter, and the project was placed in the do-it-yourself column.
It was challenging to find a large capacity water heater. Local stores were not helpful and I ultimately ordered an AO Smith 75,000 BTU power vent water heater from a New Jersey supply house. The efficient power vent unit would allow placement of the water heater on the main floor without a vent to the roof. Instead the power vent allows for venting though the side wall with 3 inch PVC pipe. While I was making these decisions I found good support from my neighbor Paul who is a licensed plumber. Paul spent many years working new construction, but since I've known him he's been maintaining the facilities of the ancient locomotive barn used by Utah Transit for servicing their fleet of diesel locomotives. His depth of knowledge and experience is phenomenal, and he graciously offered to help install the new water heater. I was particularly pleased with that, since I would not be comfortable doing plumbing for natural gas. I originally hired someone for that part of the installation years ago. At that time, I did learn how to solder the copper pipe that is used in the heating system, and Paul said I did good with it, since none of the joints leaked. BUT: Paul's work looks so much better!
For the downstairs installation, I chose to put the heater beneath the stairs in the storage room (where it should have been in the first place).

Supply and return copper piping needed to be rerouted. Black iron pipe for the natural gas supply needed to be rerouted. A new PVC venting to the rear side wall of the shop needed to be installed. To minimize Paul's time I wanted to have all the access holes prepared. I also realized that I'd want to prepare all of the lengths of iron pipe required for the job. I've worked with iron pipe before, but my approach to determining lengths has been rather casual. Since I'd be working with a master plumber, a casual approach was not going to work. With the help of Google, I learned the technical art of determining "fitting allowances" and ordered seven lengths of cut and threaded pipe from a local plumbing supply house. I'll admit that they laughed at me when I specified lengths to the nearest 1/16 of an inch, but they cut all of them to my spec, except for one. I lost a little sleep over this part of the adventure but last Saturday when Paul came to help it worked out perfectly. I was Paul's assistant for two hours and the plumbing was complete.
The PVC venting created another challenge. AO Smith specified CPVC pipe for the first five feet of the vent. CPVC has a temperature rating of 190 degrees Farenheit, whereas standard PVC has a rating of 140 degrees. Little did I know that supply of 3-inch CPVC would be challenging too. After multiple local calls, I found a supply house in Ohio and they had the materials to me within four days. Thursday night the system was up and running. On Friday, my feet were warm in the shop for the first time in five weeks.
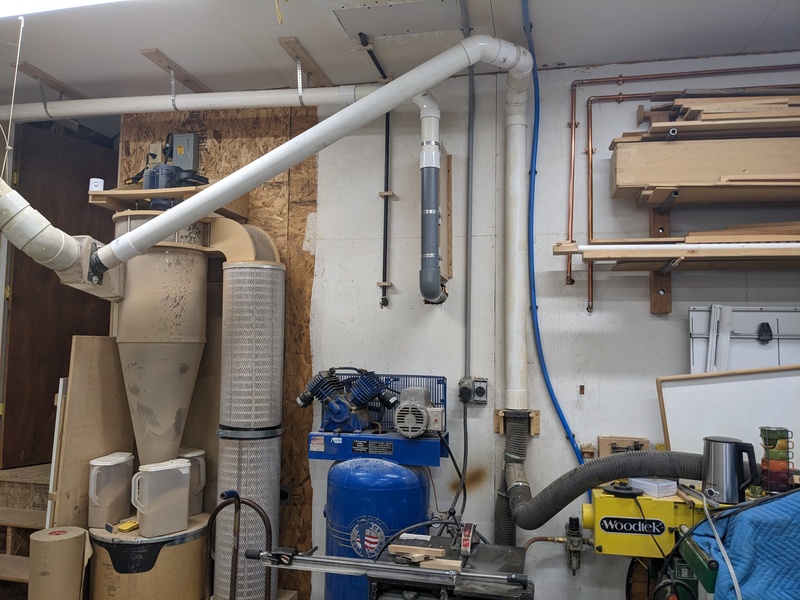
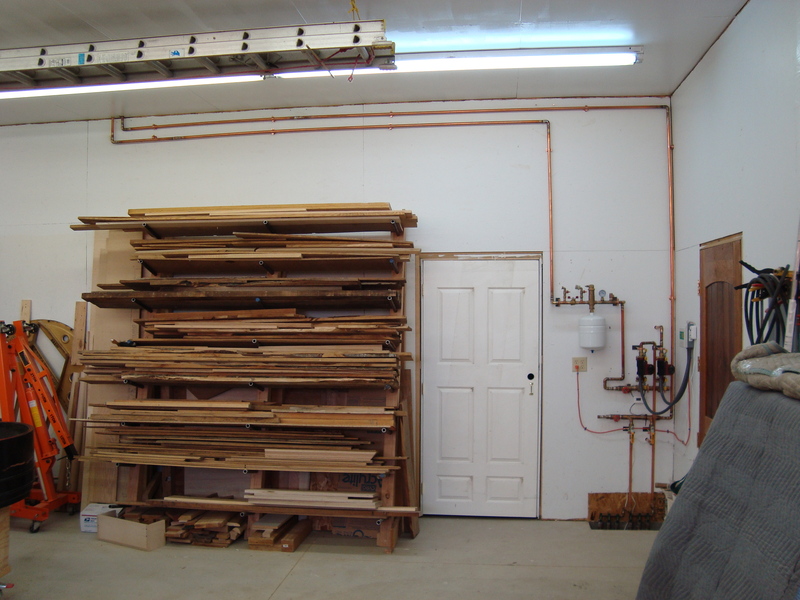
Primitive arts
I kept the shop warm for five weeks. I had work to do there, and I wasn't going to let pianos get cold. I've appreciated the occasional use of the woodstove in the shop, but I haven't used it as much as I expected. There are two reasons for this:
- I enjoy creature comforts.
- Air quality standards in Davis County Utah generally prohibit the use of solid fuel heating during times of high pollution. Those times are when it is cold!
I did my best to keep the fire running hot and clean for five weeks, but I also did not look at the daily announcements of PM 2.5 pollutant levels and burn restrictions. I'll just have to assume that I probably wasn't in compliance with the law for many of those days.
The first few days of constantly feeding the fire were enjoyable and generated fond memories of learning to split kindling with Grandpa Henkel, and carrying in wood for Grandma McGuire, and keeping warm in Dad's shop. But after those first few days, it became a chore. An habitual chore that I was pleased to set aside on Friday.
So the shop is warm again, and spring is arriving.
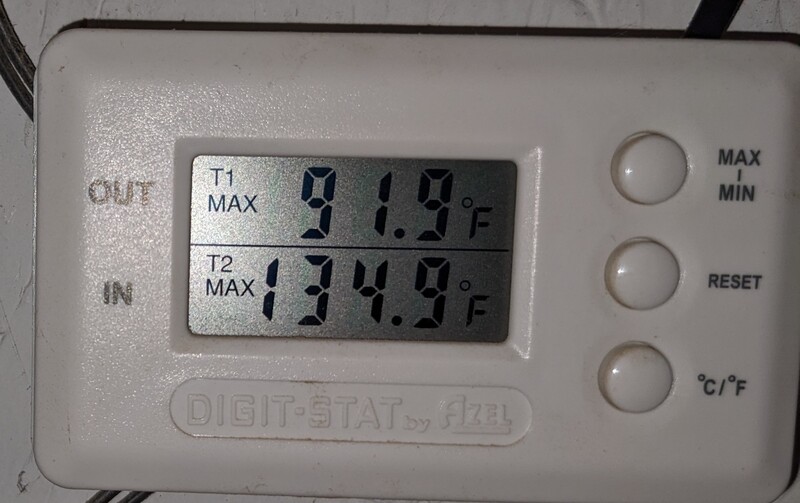
2025 2024 2023 2022 2021 2020 2019 2018 2017 2016 2015 2014 2013 2012 2011 2010 2009 2008 2007 2006 2005 2004
Comments
I welcome your comments. You do NOT need to sign in to leave a comment. If you create an account and sign in, my comment system will notify you of replies to your comment. Thanks for stopping by.--Duane McGuire